How we produce our fabrics and garments
Charaka produces naturally dyed handloom fabric, saree, stole, towel, bed linen, home furnishing and garments. Charaka produces on an average of 30,000 meters of naturally dyed handloom fabric per month. This is probably a national record in the country. Charaka believes in sustainability and follows rain water harvesting, open well and solar lighting facilities at its production facility. Charaka is a success story.
Production Process at Charaka
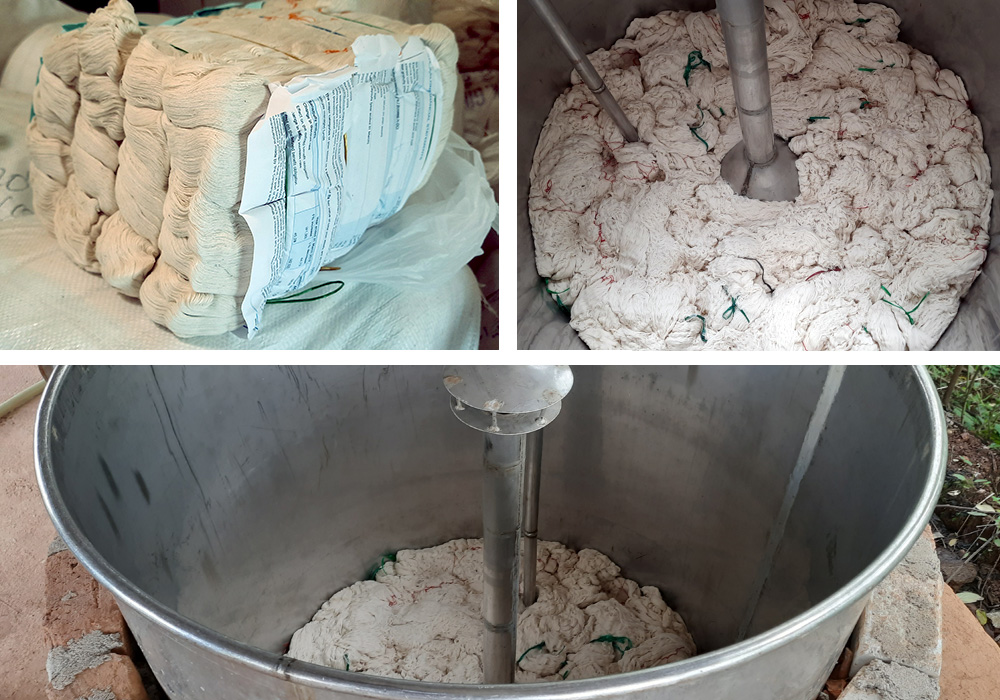
Yarn Procurement
Procurement of Cotton Yarn from spinning mills, Yarn of different counts (i.e., 2/40, 2/60, 20, 30, etc.)
Yarn Scouring
Main purpose of yarn scouring is to remove natural and artificial impurities from the fabric, making the yarn cleaner and more absorbent for the next process.
Cotton yarn, in particular, has fewer impurities. Cotton yarn contains non-cellulosic substances such as dust, oil, wax, minerals and many impurities as well. So the way of removing those impurities is called scouring. The most important wet process used on textile products before dyeing or printing is scouring.
Natural Dye
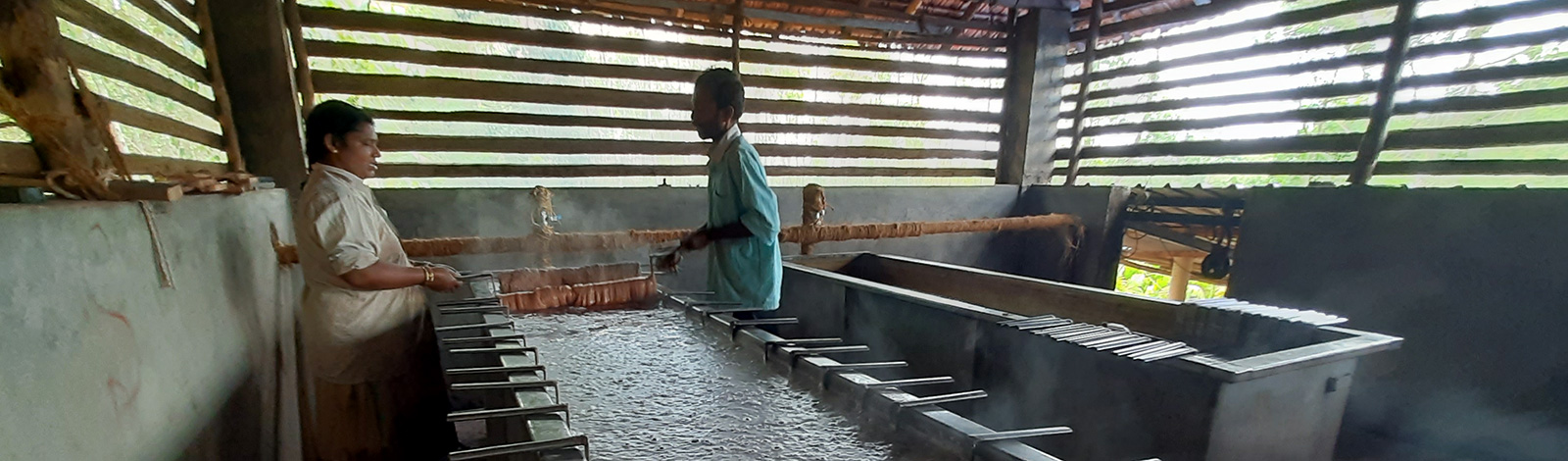
Natural Dyeing is the process of using natural dyes that are extracted from natural sources, such as plants and minerals. You can extract beautiful colors from fruits and vegetables. Every step of the process is very important and must be done in the right order.
Charaka has successfully worked to revive traditional natural dyeing techniques. The dye ingredients are plant-based, and include materials such as arecanut liquid, pomegranate peel, madder root, eucalyptus leaf and indigo.
Bobbin winding
In the process yarn in the hank form is wound on bobbins. This is the first step in transforming the yarn from the hank form to a linear form. Dyed hank yarn is wound on bobbins with the help of Charkhas. This process enables the laying out of yarn lengths for weaving. Bobbin winding is done by women in the weaver households.
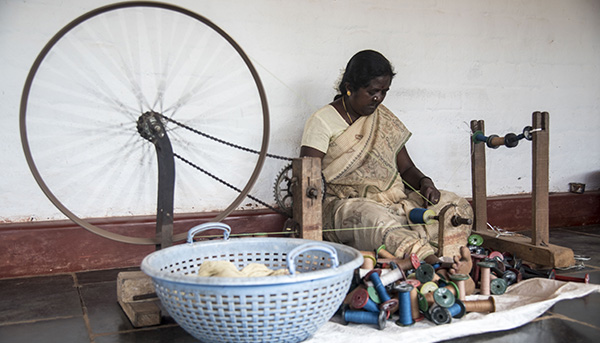
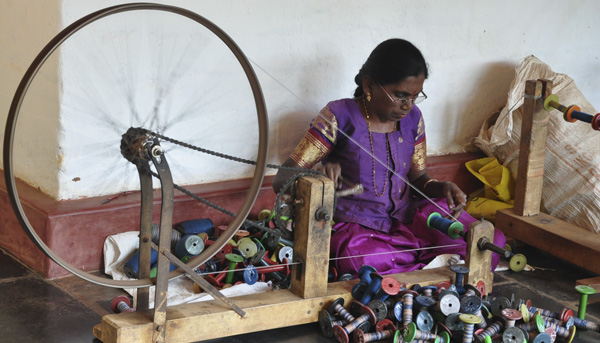
Warping
The parallel winding of warp ends from many winding cones onto a common Warp Beam is called warping.
The warp is a set of threads attached to the loom lengthwise before weaving begins. Warping is the process of creating the base yarn that runs along the length of fabric through which the “weft” yarns are filled in to make the fabric.
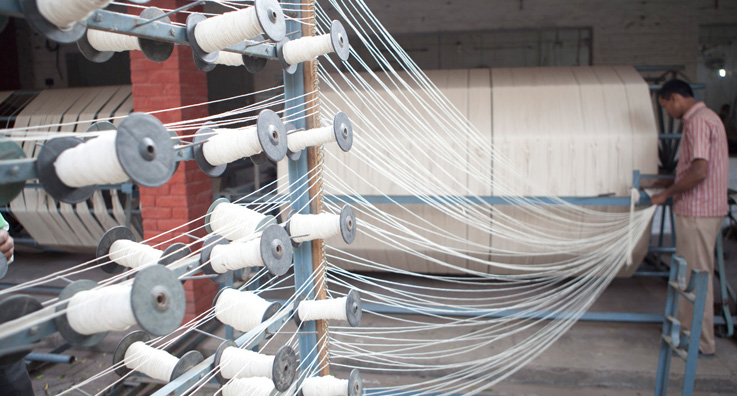
Weaving
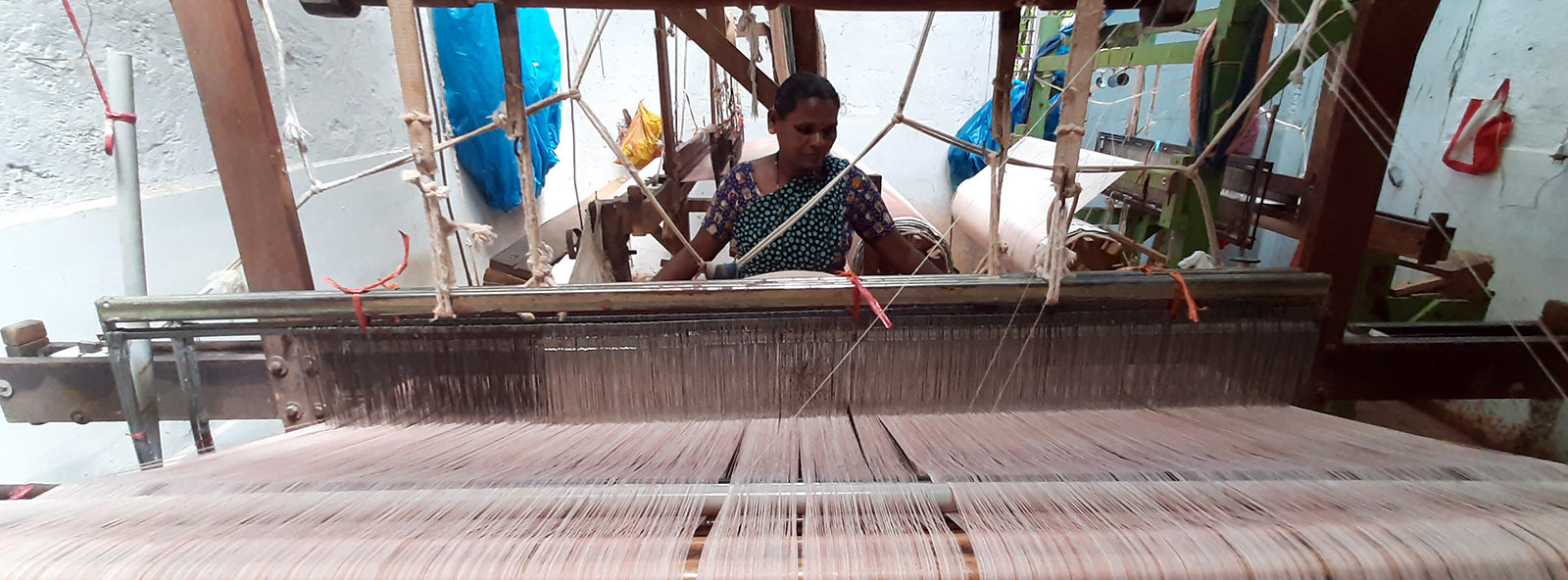
Shrinkage and Ironing
Shrinkage is described as the reduction in length and width of the cloth when washed. Therefore all fabric should be subjected to shrinking before cutting and sewing. Shrinkage can be carried out in different methods. They also vary from fabric to fabric. Ironing is done after the shrinkage so that it is easy for the garment cutting process.
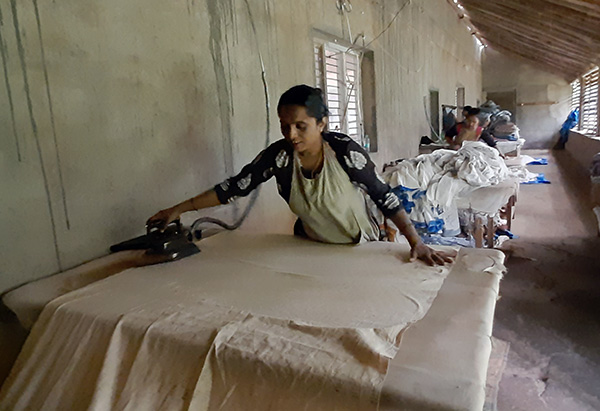
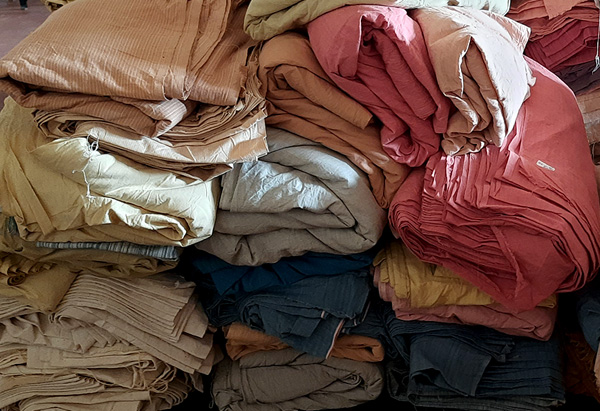
Cutting and Tailoring
Ready fabric is used to start this process of cutting. Cutting for various readymade garments is done. Once the cutting is done, it moves to the Tailoring department for stitching of the garments. Garments stitched are quality checked, Ironed and ready for dispatch
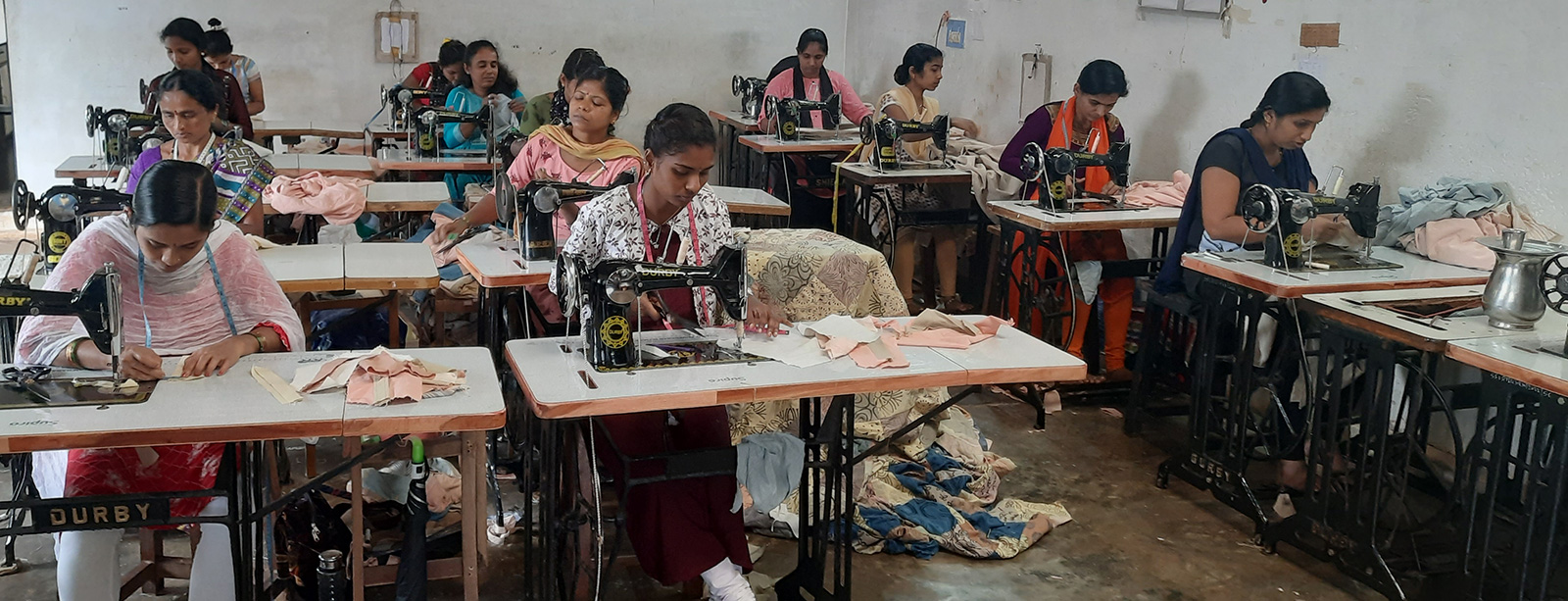
Quality
With the quality inspection at diffrent levels, our production follows strict inspection process. Inspection, in reference to quality management can be defined as the visual examination partially finished components of the garments and completely finished garments in relation to specifications, or requirements, as well as measuring the garments to check if they meet the required measurements. The term “requirements” sometimes is used broadly to include standards of good workmanship.
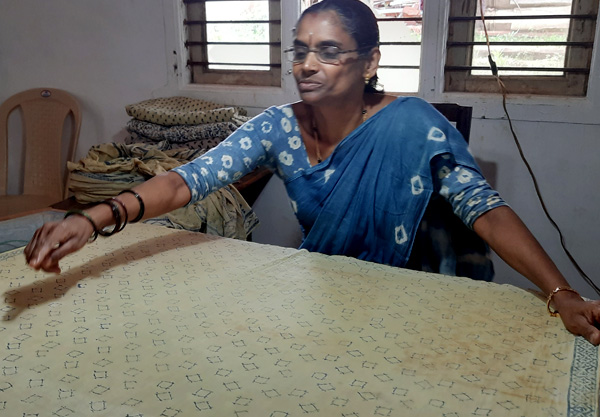
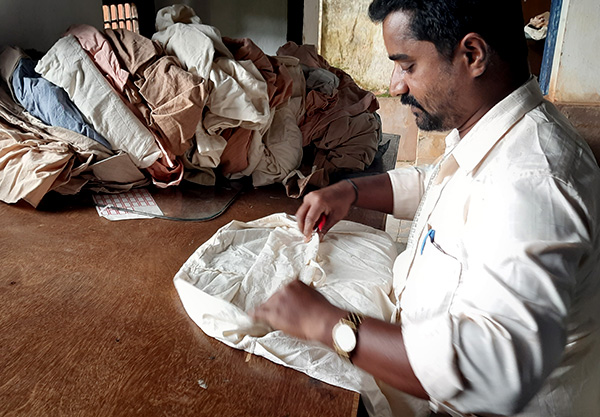